New definition of oil separation
The new ProVent² generation from MANN+HUMMEL offers smart solutions for blowby gas oil separation for all diesel engines with an engine capacity between 2.9 and 80 liters.
Basics of crankcase ventilation
Increasing awareness regarding environmental and health protection is leading to ever stricter emission limit values for the diesel engines used in construction machines, agricultural machines, mining operations and marine applications. In addition to exhaust gases, emissions from the engine crankcase can contribute significantly towards the overall emissions of the engine. The reason for emissions from the crankcase is a leakage gas flow, called blowby, which occurs at piston rings, valve shafts and the bearings of the turbocharger which is enriched though condensation and atomization with small oil droplets. In order to avoid an uncontrolled outflow from the crankcase, this gas flow has to be removed via crankcase ventilation.
If the blowby gas is released directly to the ambient air, the process is called open ventilation. However, in order as much as possible to avoid emissions from the crankcase, in modern engines the trend is towards closed crankcase ventilation where the blowby gas is returned to the intake channel of the engine. Using a separator which is integrated in the crankcase ventilation, the oil droplets are separated from the blowby gas and the oil is returned to the oil sump. In the closed crankcase ventilation process, the efficiency of the separation is particularly significant because the components in the intake channel such as the turbocharger, intercooler and inlet valves have to be protected against contaminants contained in the oil from the blowby gas.
With its new ProVent² range, MANN+HUMMEL now offers some ingenious solutions. With its modular design and two different housing concepts, the series is able to cover engines with an engine capacity between 2.9 and 80 liters, with easy and flexible solutions to meet many different customer requirements.
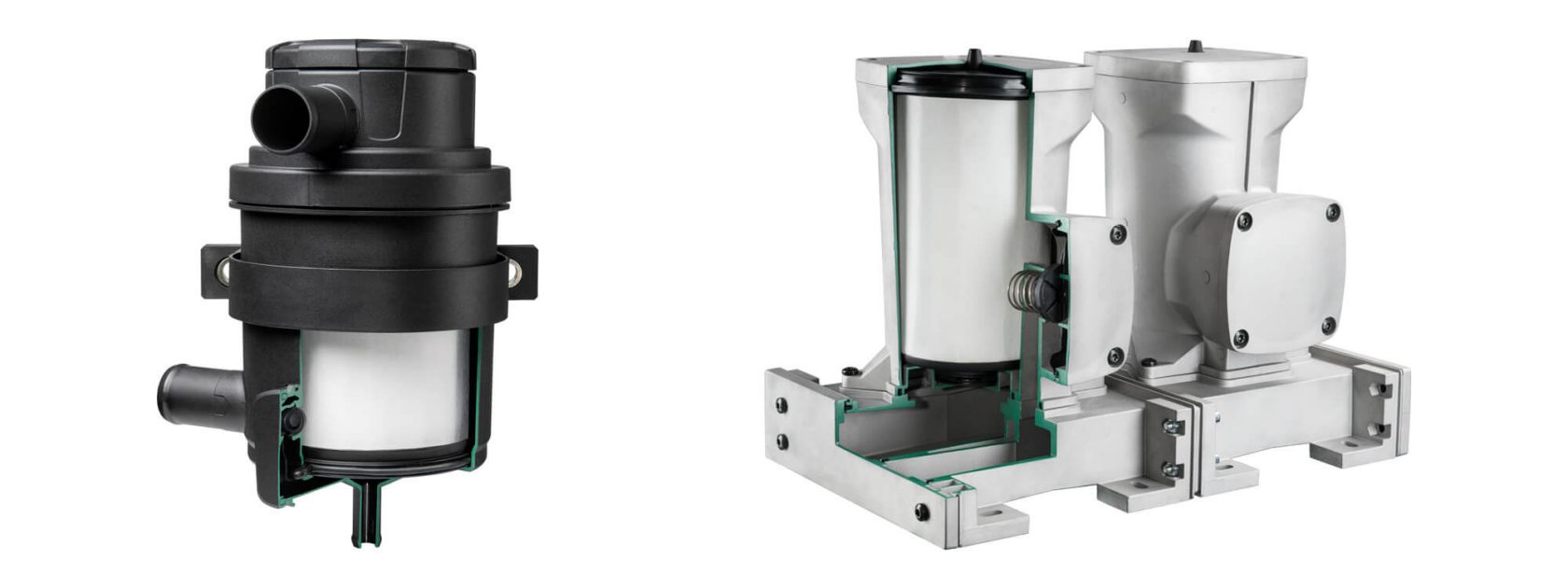
High-efficient solution and improved service life
Non-automotive diesel engines designed for long operating hours and high loads present a special challenge when it comes to the cleaning of the blowby gas. Due to the fact that such engines have continuously high local temperatures, oil evaporates to enrich the blowby gas. As a result, the oil droplets contained in the gas have to be removed in addition to the gas itself. The difficulty is the size of the oil droplets, with high power density engines having even smaller droplets. This stretches the possibilities of conventional inertial separators. They achieve their best results with large drops with a diameter starting with a micrometer due to the relatively still high mass inertia. But for smaller droplets they are no longer physically able to realize the required separation efficiency of over 90 percent. So-called fiber separators are recommended here which exploit the principle of coalescence. All the filter elements of the ProVent² range are fitted with a highly‑efficient separation media which has a specially designed fiber structure. In the development process, the experts at MANN+HUMMEL were able to use their extensive experience with oil mist separation. They improved the structure of the developed separation media to also take into account porosity and fiber distribution. The result is a coiled filter element with a high-efficient media made from glass fiber and a non-woven fabric. After several thousand operating hours, field trials and engine tests indicate an insignificant increase in pressure. The ProVent² range therefore impresses with a service life which is up to eight times longer than comparable solutions.
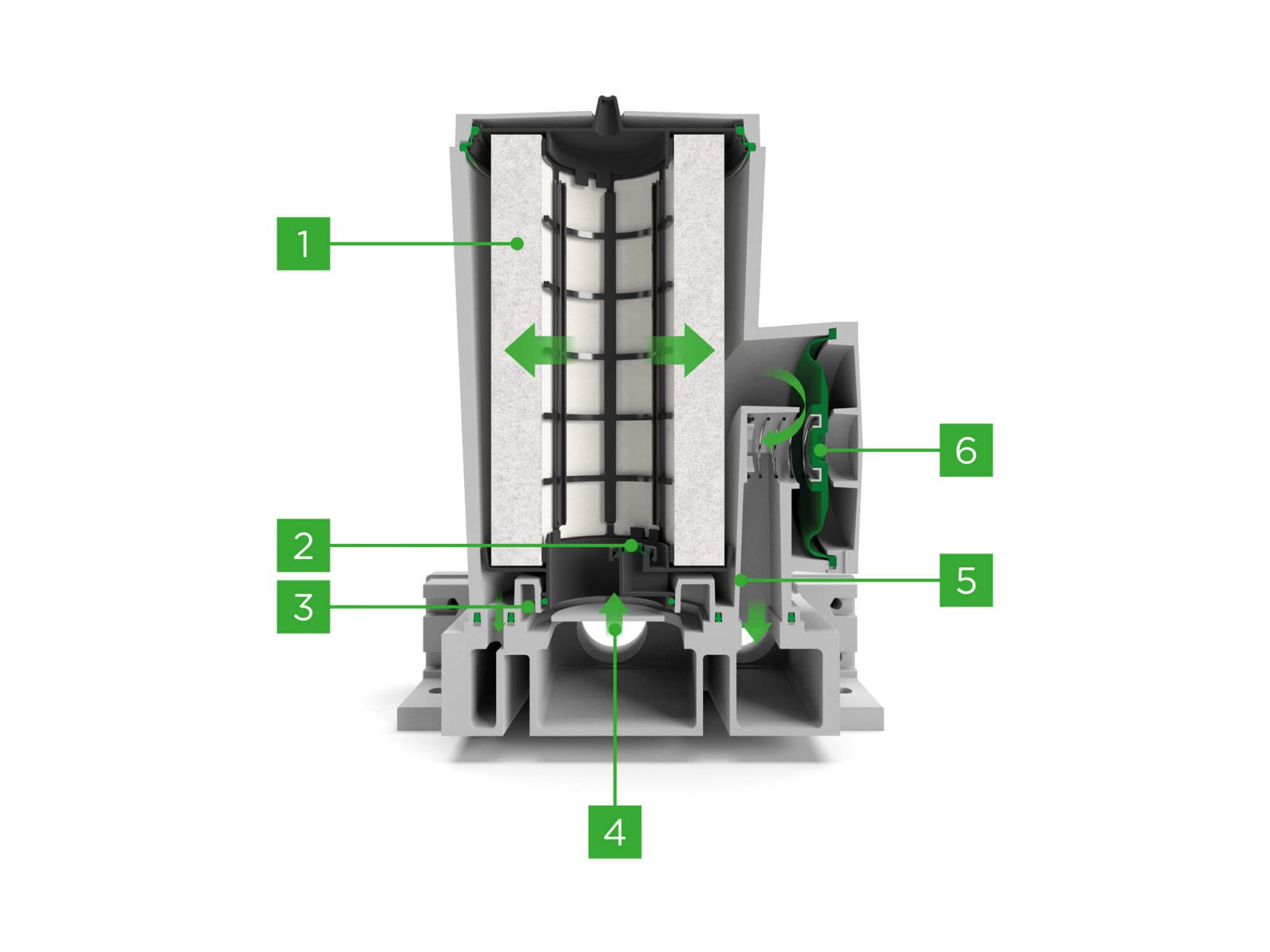
1 Oil separator
2 Bypass valve
3 Oil return
4 Dirty gas inlet
5 Clean gas outlet
6 Pressure control valve
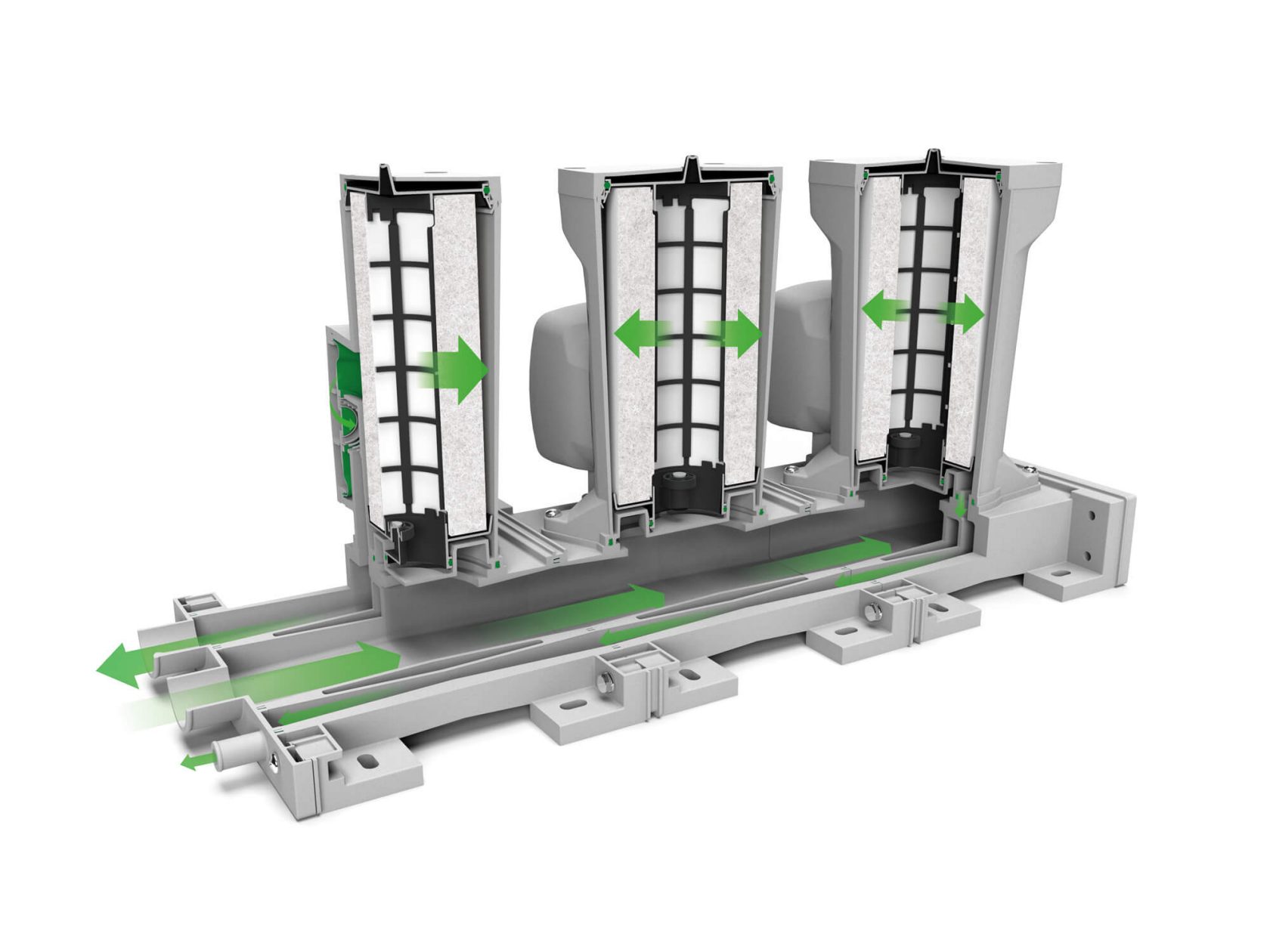
Modular system offers excellent flexibility
The platform strategy pursued by vehicle manufacturers leads to many engine variants. Using the option of parallel operation of the ProVent2 100 to 300 or simply the extendibility of the ProVent2 500, the system can be adapted to different volume flow rates and also to different requirements regarding pressure difference and the service interval. While the market volumes for the ProVent² 100 to 300 are high enough to justify a plastic housing, the market for large engines is characterized by lower volumes. In order to cover different power classes and application-specific load profiles with an appropriate efficiency, MANN+HUMMEL has in addition developed a modular crankcase ventilation system made from die-cast aluminum.
As a result, the modular designed ProVent² 500 variant for engines in approx. the 2,500 kW power class consists of three parts. Each part again consists of two parts: a basic module and a separation and control module. The basic module has flow channels for the dirty gas loaded with oil droplets, the clean gas and the return of the separated oil. Depending on the engine size, a number of these basic modules can be easily mounted one after the other. The actual coalescer is positioned on the basic module. The dirty blowby gas enters the basic module from below into the coalescer and flows through it from the inside to the outside, whereby the aerosol is separated with high efficiency by the filter media. The separated oil then flows through the oil return channel back to the oil sump of the engine.
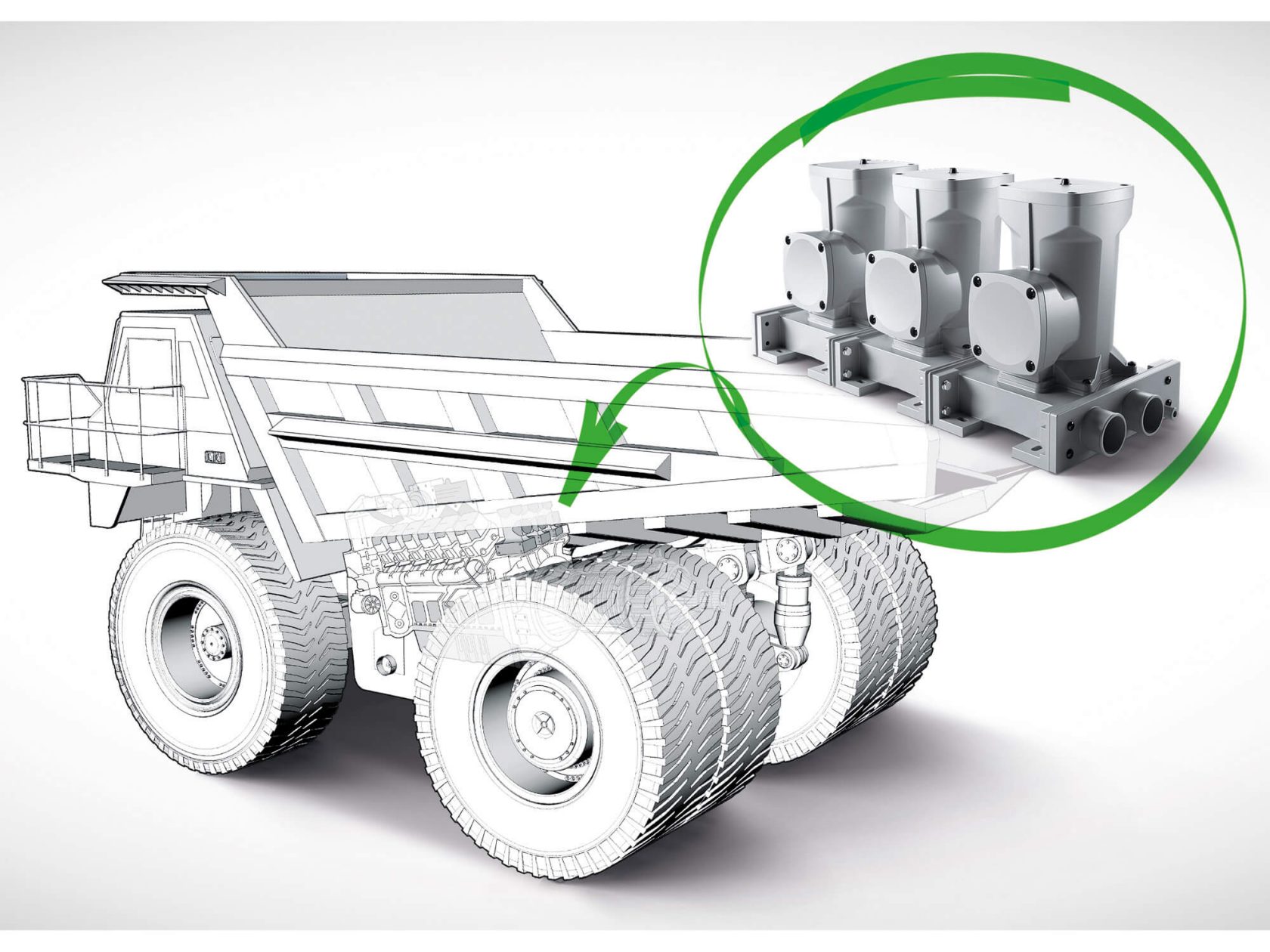
Quick installation
A priority for MANN+HUMMEL was also to design the ProVent² range to be easy to install and service. As the pipes to and from the engine are the only necessary interfaces to the engine, the crankcase ventilation system can be flexibly mounted on or near to the engine. ProVent² is therefore a tailor-made solution for crankcase ventilation which was specially developed for non-automotive diesel engines. Due to its modular design, it offers excellent flexibility and can easily be adapted to many different engines with an engine capacity between 2.9 and 80 liters.