System expertise for fuel cell powertrains
Legislation governing vehicle emissions is becoming stricter, the climate debate and therefore also the development of alternative drives is gaining momentum. One promising solution is the fuel cell used to supply energy to an electric drive. MANN+HUMMEL has now developed an innovative air induction system for the cathode path in order to ensure an efficient supply of clean air to the fuel cell.
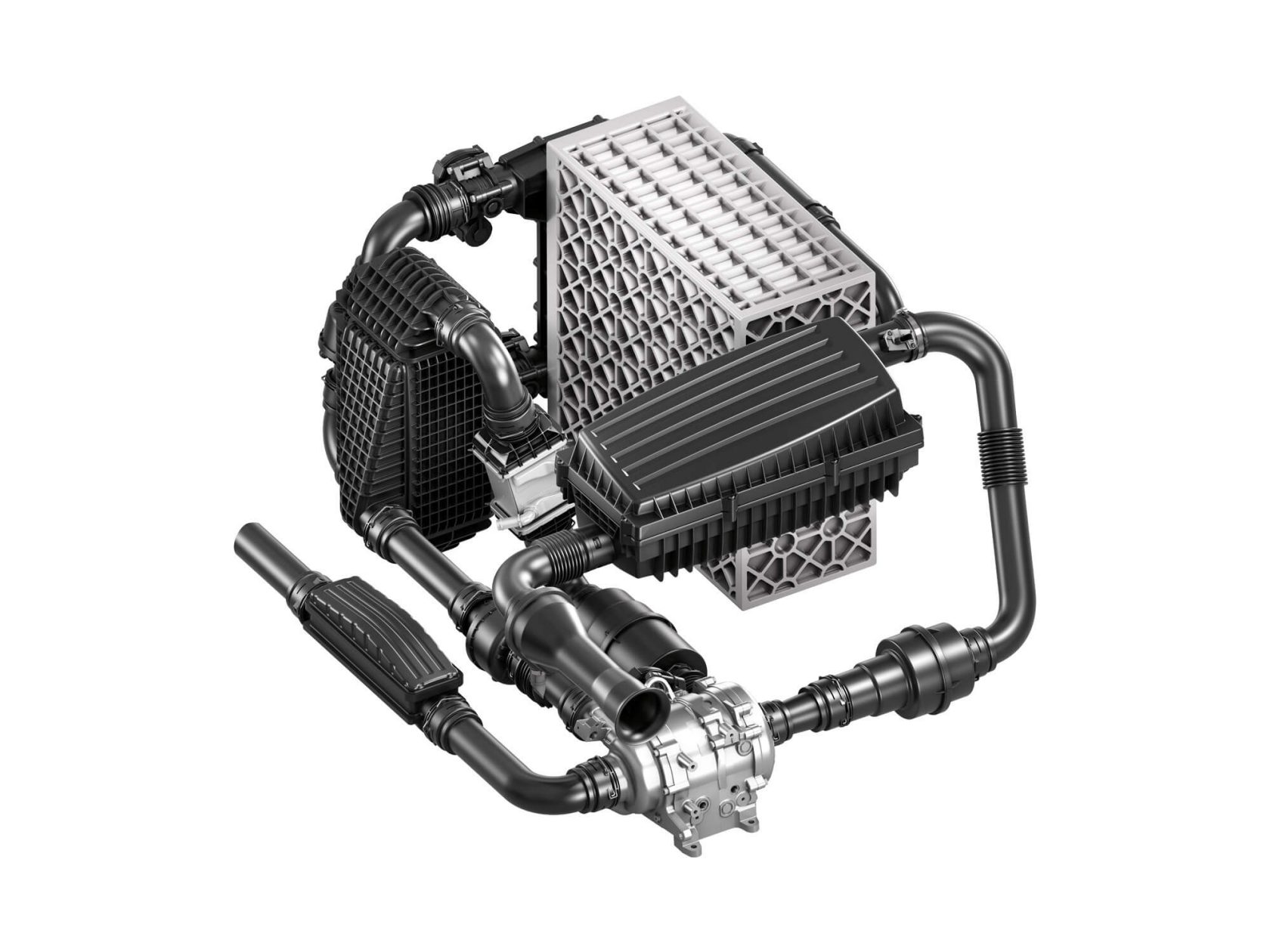
A proton exchange membrane (PEM) fuel cell consists of electrodes which are separated from each other by a semi-permeable membrane. Inside the fuel cell an electrochemical reaction converts hydrogen (H2) and oxygen (O2) into electrical energy. The protons are able to permeate the membrane and as a result the unit is able to generate an electric current.
A large number of these electrode membrane units arranged in series form the fuel cell stack. During operation, the core components are highly sensitive to particles, harmful gases and water present in the intake air. In addition, the proton exchange membrane requires a sufficiently high level of relative humidity in the process air to ensure that it does not dry out. Furthermore, harmful gases can cause irreversible damage to the catalyst which is coated with platinum. In order to ensure trouble-free operation and system lifetime, the filtration of particles and the adsorption of harmful gases is therefore equally important as efficient water separation. These requirements are met by the air induction system newly developed by MANN+HUMMEL for the cathode path of the fuel cell.
Clean fresh air
The ambient air sucked in is guided through the dirty air duct with water separator to the cathode air cleaner, a core element of the whole system. A particle filter layer separates particulate matter from the intake air. Dedicated activated carbon layers of the filter element adsorb harmful gases such as sulfur dioxide (SO2), nitrogen oxide (NOx) and ammonia (NH3) and therefore protect the valuable catalyst of the fuel cell against contamination and degradation.
On the clean air side an air flow sensor determines the mass of air which enters the system. This information is used to calculate the exact ratio of oxygen to hydrogen in order to ensure optimal operation and the efficiency of the fuel cell stack. A resonator integrated in the clean air duct dampens unpleasant flow noises and bellows in the duct serve to provide the necessary motion compensation.
Perfect humidity
In order to be able to guide sufficient air to the fuel cell, the clean air passes a compressor. This leads to an increase in temperature. Before entering the fuel cell stack, the air temperature is reduced in the charge air cooler located downstream of the compressor. A sufficiently high level of humidity is necessary for the optimal operation of the fuel cell. If the intake air is too dry, this will have a negative effect on the conductivity of the proton exchange membranes in the fuel cell stack. Depending on the operating status, the humidifier therefore adds process water from the cathode air exhaust to the intake air to increase the humidity. As a result of the process, water droplets may form which are separated by a cathode water separator to protect the stack.
The inlet control flap upstream of the stack regulates the air flow to ensure it is ideal for the electrochemical reaction. A particle filter in the media distribution module, a flange to the fuel cell stack, also provides additional protection against particles which originate from manufacturing and assembly processes.
The final step
The water produced by the reaction is guided by an exhaust duct back to the humidifier. This is where the humidity is transferred via gas-tight flat-sheet membranes to the intake air. Excess water is removed by means of a turbine water separator to protect the turbine against water impact. The turbine is used to exploit the kinetic energy still present in the system and therefore increases overall efficiency. A resonator dampens undesirable noises before the air is guided out of the exhaust duct.
In addition to the air induction system, MANN+HUMMEL has also used its filtration expertise for the cooling circuit. The reaction of hydrogen and oxygen in the fuel cell generates heat which has to be removed. The coolant particle filter separates harmful particles in the main flow from the coolant circuit and therefore protects the pump. The ion exchange filter located in the bypass flow ensures that the increased electrical conductivity of the coolant caused by the discharge of ions from the system remains below the permissible limit.
In the development of the air induction system for the cathode path of the fuel cell, the experts at MANN+HUMMEL were able to make use of their simulation expertise and on extensive know-how with regard to the design of components. The result is a fully integrated system supplied by a single supplier. Perfectly matched components and the significant reduction of interfaces simplify processes and ensure the performance of the fuel cell over its entire lifetime.